Understanding the Art of Welding: How to Stay Clear Of Undercut Welding Issues for Flawless Manufacture Results
Efficiency and precision are critical on the planet of welding, where also the tiniest blemish can compromise the architectural integrity of a produced item. One typical challenge that welders face is damaging, a flaw that can lead and compromise a weld joint to expensive rework. By understanding the source of undercut welding and executing reliable methods to avoid it, welders can boost their craft to new degrees of excellence (Preventing weld undercut). In the search of remarkable fabrication outcomes, mastering the art of welding to prevent undercut concerns is not simply an ability yet a need for those pursuing perfection in their work.
Understanding Undercut Welding
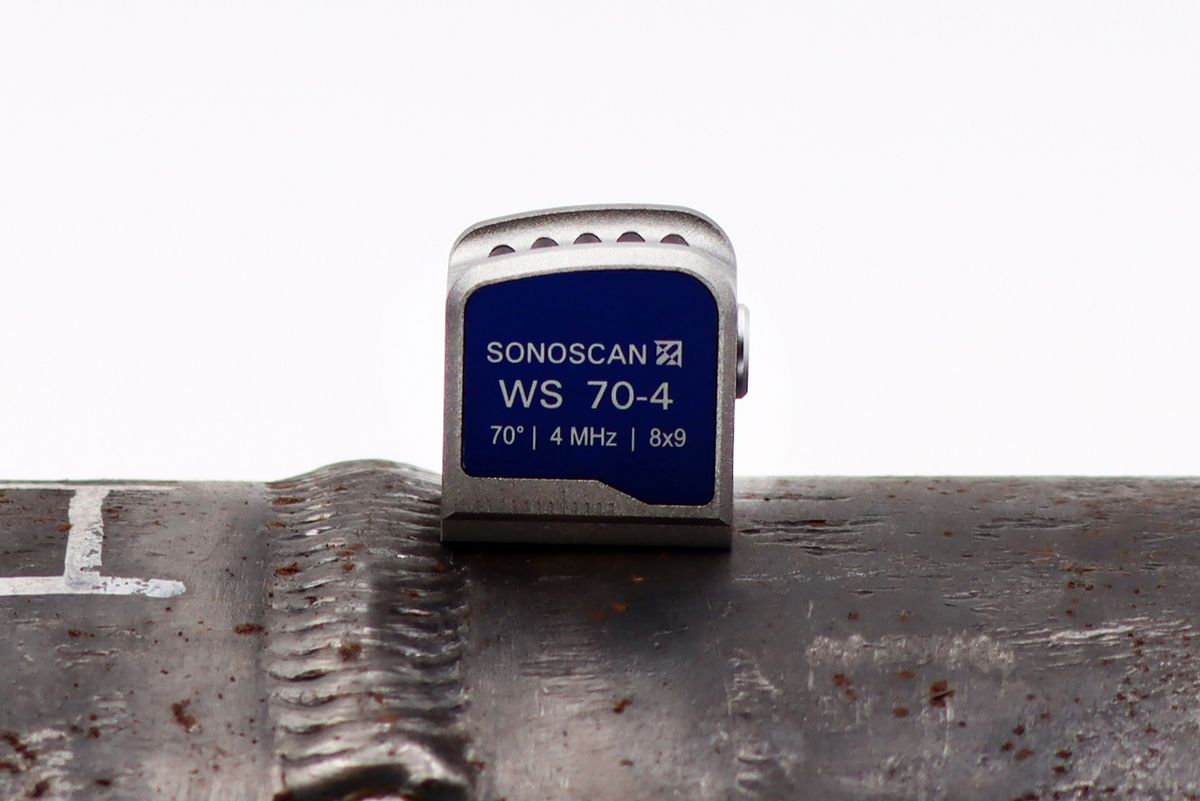
To stop undercut welding, welders must make certain correct welding criteria, such as adjusting the current, voltage, travel speed, and maintaining the proper electrode angle. By understanding the causes of undercut welding and executing preventive steps, welders can accomplish premium, structurally sound welds.
Sources Of Undercut in Welding
Understanding the elements that add to damage in welding is essential for welders to produce high-quality, structurally audio welds. When the weld steel does not appropriately fill up the groove formed in between the base steel and the previously deposited weld steel, undercutting occurs. Several variables can cause undercut in welding. One common reason is extreme heat input. Welding at heats for extensive periods can result in the base steel thawing more than desired, leading to undercut. Inadequate welding incorrect or existing welding speed can also add to undercut. Not enough current may not supply enough warmth to melt the base and filler metals adequately, while too much speed can protect against appropriate fusion, triggering undercut. Additionally, inappropriate electrode angles or incorrect lantern control strategies can produce locations of low weld steel deposition, promoting undercut. Recognizing these causes and implementing correct welding methods can aid stop undercutting problems, ensuring solid and durable welds.
Techniques to Protect Against Undercutting

To minimize the threat of damaging in welding, welders can utilize calculated welding methods aimed at enhancing the quality and honesty of the weld joints. In addition, utilizing the right welding method for the particular joint configuration, such as weave or stringer grains, can add to minimizing undercutting.
Additionally, proper joint prep work, consisting of making sure tidy base materials devoid of contaminants and using the appropriate welding consumables, is essential in preventing undercut issues. Utilizing back-step welding methods and controlling the weld grain profile can also aid distribute heat equally and reduce the risk of undercut. Normal evaluation of the weld joint during and after welding, along with carrying out high quality guarantee procedures, can aid in attending to and spotting damaging issues without delay. By her comment is here executing these strategies carefully, welders can achieve flawless fabrication results with marginal undercut problems.
Importance of Correct Welding Parameters
Choosing and maintaining suitable welding specifications is vital for achieving effective welds with minimal issues. Welding criteria refer to variables such he has a good point as voltage, current, take a trip speed, electrode angle, and securing gas circulation rate that directly influence the welding procedure. These parameters must be meticulously adjusted based upon the sort of material being bonded, its density, and the welding strategy used.
Appropriate welding parameters make certain the right amount of warm is put on melt the base metals and filler material uniformly. If the specifications are set too high, it can result in extreme heat input, causing distortion, burn-through, or spatter. On the other hand, if the criteria are also reduced, insufficient combination, lack of penetration, or damaging might happen.
High Quality Assurance in Welding Workflow

Verdict
Finally, grasping the art of welding requires a comprehensive understanding of undercut welding, its reasons, and strategies to stop it. By ensuring correct welding specifications and executing quality assurance practices, remarkable manufacture outcomes can be accomplished. It is crucial for welders to continually strive for quality in their welding procedures to stay clear of undercut concerns and create high-grade welds.
Undercut welding, a typical flaw in welding processes, happens when the weld steel does not correctly load the groove and leaves a groove or anxiety along the welded joint.To stop undercut welding, welders should make sure appropriate welding specifications, such as readjusting the existing, voltage, traveling speed, and preserving the appropriate electrode angle. Inadequate welding wrong or present welding rate can also contribute to damage.To mitigate the danger of damaging in welding, welders can use tactical welding methods intended at enhancing the high quality and stability of the weld joints.In verdict, mastering the art of welding needs a thorough understanding of undercut welding, its causes, and methods to stop it.